
Plugging and Abandonment Process
Plugging and Abandonment (P&A) is a process used in the oil and gas industry to safely close off wells that are no longer in use. The goal of P&A is to ensure that the well is securely sealed, protecting the surrounding land and water, and leaving the site safe for future use.
Before any field operations begin, our team of engineers conducts thorough research to determine the most effective plugging process and identify potential challenges. This includes evaluating safe access and egress, soil conditions, terrain contours, and other site-specific factors. Our team also writes a detailed plugging procedure that adheres to and exceeds state guidelines, which is then submitted to the governing body for approval.
Safety Assessment
Prior to moving any equipment on-site, we address and correct any issues to ensure a safe working environment, including leveling the pad and testing anchors. We also assess potentially hazardous atmospheres and other site-specific hazards. If such conditions are present, our Health, Safety, and Environmental (HSE) team develops a safe operating procedure to mitigate risks before plugging operations commence.
Site PreparationOnce initial removal operations are complete, we address any remaining tubulars that may be stuck in the wellbore. Before these operations commence, our site supervisors and plugging crews perform a thorough evaluation of the well, uncovering all casing valves, and monitoring and recording well pressures. Utilizing their extensive training in downhole operations and well control, our supervisors develop a detailed action plan to manage and stabilize the well before any work begins. This expertise ensures that all procedures are conducted following state safety protocols and regulations, effectively troubleshooting any issues encountered during the extraction process.
Using specialized workover rigs, we begin by pulling the rods and pump, if present, from the wellbore. To ensure safety during this process, we install a Blow Out Preventer (BOP), which helps manage well control issues by stopping the flow of over-pressured gas or liquids until a kill mud can be pumped into the well. This kill mud balances the hydrostatic pressure within the wellbore with the pressure of the fluids from the surrounding formations, preventing uncontrolled flow.
After securing the well with the BOP, we proceed to remove the tubing. If the tubing is found to be stuck due to various wellbore conditions, we employ specialized fishing tools to attempt to free it. In cases where the fishing tools are unsuccessful, we use tubing jet cutters based on pipe stretch calculations to precisely cut the tubing above the point where it is stuck, maximizing the amount of material we can safely remove from the wellbore.
Fishing and Tubular ExtractionAfter clearing the wellbore, we begin the plugging process by setting a Cast Iron Bridge Plug (CIBP) to isolate the well from any producing formations. This initial barrier is crucial for controlling the well and preventing fluid migration. Following the placement of the CIBP, we commence the cementing operations, selecting different classes of cement based on the depth and geological conditions of the well.
The primary goal is to create a series of cement plugs that effectively separate different producing zones and, most importantly, protect groundwater sources from contamination by hydrocarbons. These plugs can be placed inside the casing or, when necessary, set both inside and outside the casing using through-tubing perforations. After setting each plug, we rigorously test its integrity and wait for the cement to cure. Once the cement is cured, we tap the top of the plug to confirm it is at the correct depth.
To ensure the wellbore is properly sealed, we perform a casing integrity test after setting the CIBP. The results guide any necessary adjustments in our procedures to guarantee that future cement plugs are placed accurately to cover all approved zones.
Throughout the process, we maintain well control by using an approved 10-pound circulating fluid to keep the well balanced. Depending on the well information and cement bond logs, we may perforate the production casing with specialized explosives to place a calculated balanced squeeze plug. This ensures complete coverage both inside and outside the production casing. Our site supervisors, who are thoroughly trained in handling explosives and adhering to safety protocols, oversee this operation to ensure the safety of our personnel and the environment. We maintain well control at all times using written procedures, a full wellbore of circulating fluid, and tested pressure control equipment.
Cement PluggingWith all cement plugs securely set, we remove the wellhead and associated flowlines. If not needed, surface equipment like tanks and separators are also removed, following strict environmental safety standards. We use a hydrojet casing cutter to cut the wellhead six feet below the surface and cap the well, ensuring compliance with regulatory requirements.
Site and Equipment ClearanceThe final step involves restoring the site to its natural state or as close as possible. We achieve this by either burying location material below the topsoil or hauling it to an oilfield waste site, matching the natural grade and ensuring the well poses no future environmental or safety risks.
Surface Reclamation
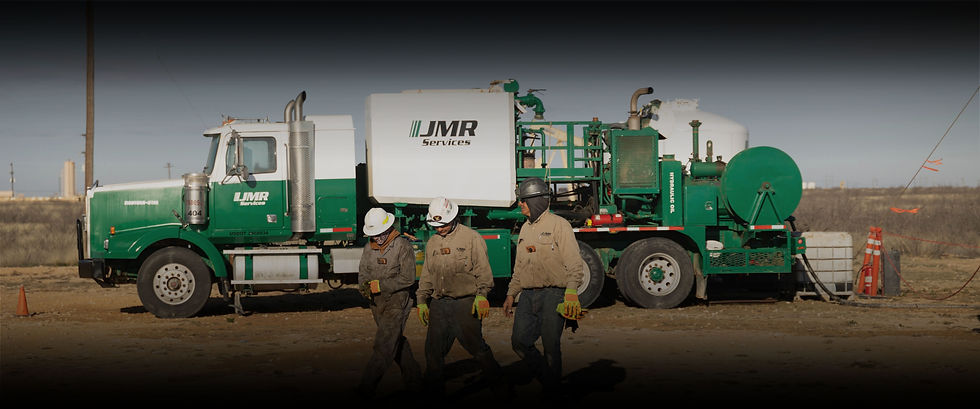